Die-cast Mold Design for New Energy Vehicle Motor Housings (Part two)
3. The application of the mold
After three batch production tests on the machine, three sets of process parameters were optimized for small batch production. The die-casting process parameters are shown in Table 2.
Table 2 Die-cast process parameters
Mold temperatures/°C |
Inner gate speeds/(m.s-1) |
Pouring gate ratio (injection head areas/pouring gate areas) |
Cylinder filling rates (volume of molten aluminum/effective volume of cylinders)% |
Aluminum liquid temperatures /°C |
Casting pressure
/MPa
|
190 to 205 |
46 |
9.2 |
50 |
660 |
110 |
205 to 220 |
55 |
9.2 |
35 |
650 |
120 |
180 to 195 |
40 |
9.2 |
40 |
680 |
100 |
Three groups of die-cast process parameters were used for trial production of 1000 pieces each, and the external quality and CT scanning of the motor shell castings were inspected and the average value of the production cycle was counted. The conclusions are shown in Table 3. The wall thickness of shell castings varies greatly, and the heat storage in different parts of the mold is different. The thicker the wall thickness is, the greater the heat storage becomes. The test results show that the temperature of the wall thickness of the mold greater than 10 mm is most reasonable to control at temperatures between 180 and 195℃. It is most reasonable to control the mold temperature at 195 to 205℃ for parts with a wall thickness of 4 to 6 mm. The speed of the inner runner directly affects the filling time, service life of the mold, and surface quality of castings. Too fast speed will prematurely erode the mold surface. There is a lot of gas entrainment of molten aluminum in the injection process, and at the same time, it will cause the exhaust to be unblocked, resulting in defects such as gas holes in the casting. When the speed of the pouring gate is 46m/s, the appearance and internal quality are the best, as shown in Figure 10.
The pouring gate ratio is the key parameter to control the filling speed and pressure transmission, which is designed after CAE simulation analysis; the third group of process parameters is the best in production efficiency, but the pass rate is low. Considering comprehensive production efficiency and quality, the first group has the best process parameters. The largest diameter of the top ten internal defects in the casting is 1.539 mm, and the porosity rate is 3.5%.
Table 3 Production Statistics
Parameter groups of die-cast processes |
Quality pass rates of castings/% |
Internal Quality of Castings (Porosity)% |
Production beat/s |
1 |
99 |
3.5 |
85 |
2 |
95 |
5 |
93 |
3 |
96 |
3.9 |
83 |
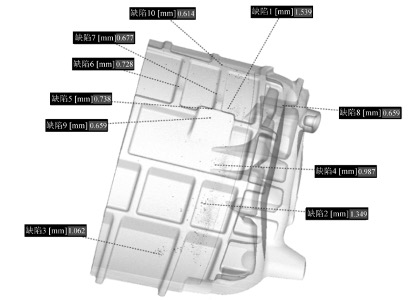
Figure 10 The CT report of the motor housing
4. Conclusion
(1) 3D printing additive manufacturing technology can provide good technical support for the design and manufacture of die-cast molds, realize the conformal cooling of complex structural parts of the mold, and completely solve the defects of die-cast parts such as aluminum sticking, mold drawing, and gas holes. The minimum diameter of the water channel can be 1 mm by 3D printing, and the distance from the mold surface can be within 8 mm to achieve precise cooling of the mold.
(2) Use thermal sensors, solenoid valves and mold temperature control systems of die casting machines to control the working temperature of the mold, and directly connect the mold temperature information with the cooling water flow control information to realize intelligent control of the mold temperature and has reference significance and application value for auto parts with similar complex structures.