2.3
Analysis of intermetallic compounds
Figure 8 SEM images of intermetallic compounds in the alloy
Figure 8 is the SEM image of the intermetallic compound in the alloy. It can be determined from XRD and metallographic structure that the rheological
die-cast ADC12 aluminum alloy is mainly composed of α-Al, Si, and Al2Cu phases. There are some unknown intermetallic compounds with different morphologies. Compounds with different shapes can be determined according to the molar ratio: the white polygon is α-Al15(Fe, Mn)3Si2, the white Chinese character Al2Cu, the dark gray block or strip Si-rich phase, and a small amount of white thick needlesβ-Al5FeSi. Among them, Al2Cu at point 11 is mixed with part of β-Al5FeSi. In Figure 8, the number of Al2Cu in different positions is the largest, which is the strengthening phase. It is generally believed that the thick acicular β-Al5FeSi splits the matrix and reduces the mechanical properties. In the figure, most of the iron phases appear as white polygonal α-Al15(Fe, Mn)3Si2, which improves the destructive effect caused by a small amount of β-Al5FeSi.
2.4
Mechanical properties
Figure 9 shows the mechanical properties of ADC12 conventional die-cast and rheological die-cast samples sampled at the same position. The tensile strength of rheological die-cast aluminum alloy is 248MPa, which is significantly better than 210.7MPa of conventional die-cast aluminum alloy. At the same time, the change in yield strength is relatively small, and the yield strength of the two is relatively close. The elongation of rheological die casting is 2.05%, which is also slightly better than that of conventional die casting at 1.46%.
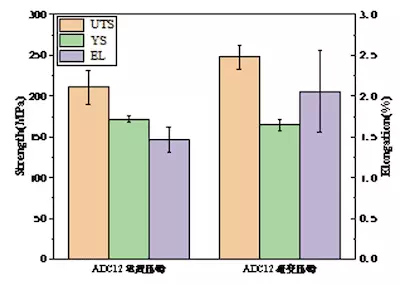
Figure 9 Mechanical properties of conventional die casting and rheological die casting of ADC12
Figure 10 is a comparison of the microstructure of conventional die-cast and rheological die-cast samples at B. In the conventional die-cast state, it appears as uniform fine dendrites and chilled grains, and there are many black micropores in it, while there are a large number of spherical or nearly spherical α-Al in the microstructure of rheological die casting; the solid phase content is high. Studies have shown that the mechanical properties of semi-solid die castings increase with the increase in the solid phase ratio, while conventional die castings are prone to air entrainment and inclusions in the filling process, which reduces the mechanical properties. The reason is that rheological die casting reduces defects such as pores inside the sample, and the structure is dense and uniform; its strength and plasticity are better than conventional die casting.
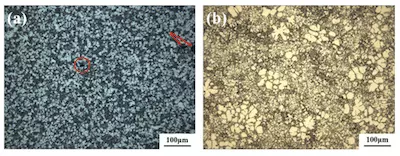
Figure 10 Microstructure comparison at the gating system B
(a) conventional die casting (b) rheological die casting
3.
Conclusion
(1) The solid-liquid interval of ADC12 aluminum alloy was determined to be 539 to 590℃, and the composition of rheological die-cast ADC12 aluminum alloy is mainly composed of Al, Si and Al2Cu phases.
(2) In the rheological die-casting process, as the distance from the pressure chamber of the die-cast machine increases, the alloy structure evolves from coarse dendrites to spherical or near-spherical grains, and the structure formation mechanism includes dendrite fragmentation and melt explosion nucleation.
(3) Determine the composition of metal compounds with different shapes. The white polygon is α-Al15(Fe, Mn)3Si2, the white Chinese character Al2Cu, the dark gray block or strip Si-rich phase, and a small amount of white thick needles β-Al5FeSi.
(4) The tensile strength of rheological die-cast aluminum alloy is 248MPa, which is better than 210.7MPa of conventional die-cast aluminum alloy. The yield strength of the two is relatively close, and the elongation of rheological die casting is also slightly better than that of conventional die casting.