Die-cast aluminum alloy parts have excellent die casting properties. The suitable alloy and die casting method can be selected according to the requirements for purposes of use, shapes of parts, dimensional accuracy, quantity, quality standards and mechanical performance as well as economic benefits.
Die casting aluminum alloy is mainly used for engine cylinder blocks, clutch housings, rear axle housings, steering gear housings, transmissions, oil pumps, water pumps, rocker covers, wheels, engine frames, cylinders, etc.
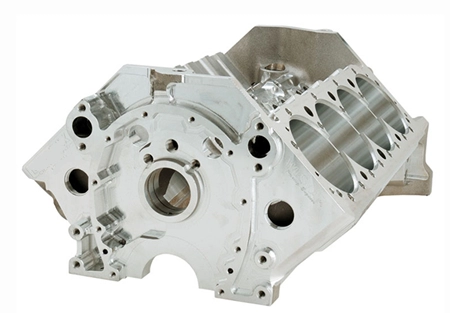
1.1
Aluminum alloy parts for engines
Automobile engines in aluminum alloy are the most lightweight; generally, the weight can't be reduced by more than 30%. In addition, the material required for cylinder blocks and cylinder heads of engines should have good thermal conductivity and good corrosion resistance, and aluminum alloy has outstanding characteristics in these aspects. Therefore, various automobile manufacturers have performed research and development of engines in aluminum. At present, many foreign automobile companies have adopted engine cylinder blocks and cylinder heads made from all-aluminum. General Motors of the United States has adopted all-aluminum cylinder jackets. French automobile company's cylinder jackets in aluminum have reached 100% and aluminum cylinder blocks have reached 45%. Japanese Nissan's VQ and Toyota's Lexus IMZ-FEV6 have adopted die-cast aluminum engine sumps. Chrysler's new V6 engine cylinder blocks and cylinder heads are made from aluminum alloys.
The German Volkswagen's advanced 6.0L W12 engine is basically made from aluminum magnesium alloy. The Audi's A8L 6.0 Quattro car adopts the W12 engine, and the weight of the car is reduced to 1980kg, which is lower than all other models. The W12 engine has 450-horsepower and 560-horsepower, and the weight per horsepower that needs to be accelerated is only 4.7kg, which is comparable to high-performance sports cars.
The Polaris series engine is GM's best engine except for the LS engine series. It is the first V8 aluminum alloy engine with overhead camshafts in the United States. Its cylinder jacket is made from all aluminum alloy by the die casting process. The 4.6-liter engine currently widely used in Cadillac has a maximum power of 320 horsepower and maximum torque of 427Nm. The supercharged models used in the high-performance V series can even reach 476 horsepower and torque of 606Nm.
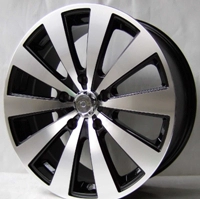
1.2
Aluminum alloy used for wheel hubs
Aluminum wheel hubs are gradually replacing steel wheel hubs because of their light weights, good heat dissipation and good appearance. In the past 10 years, the global aluminum alloy automobile wheel hubs have grown at an annual growth rate of 7.6%. According to the analysis, by 2010, the rate of automobile wheel hubs in aluminum will reach 72% to 78%. A365 is a cast aluminum alloy, which has good casting properties and good comprehensive mechanical properties. Cast aluminum alloy wheel hubs from all over the world are produced by this type of alloy. Aluminum wheel hubs which are widely used in automobiles are an example of the application of aluminum alloys to automobiles. Almost all new models adopt aluminum alloy wheel hubs.
1.3
Applications of wrought aluminum alloys
Wrought aluminum alloys are mainly used for automotive parts such as vehicles' doors and trunks, bumpers, engine hoods, muffler covers, brake systems, heat exchangers, body frames, seats, dashboards, etc.
1.3.1
Aluminum alloy for body panels
The application proportion of panels in cars continues to rise. For example, 6000 series (AI-Mg-Si series) aluminum alloy panels that have been heat-treated by T4, T6 or T8 can well meet the requirements for shells of automobiles, which can be used for the car's body frame. The body sheet metal parts of Audi A8 adopt this series of alloy aluminum materials. In addition, 2000 series (the AI-Cu-Mg series), 5000 series (the AI-Mg series) and 7000 series (the AI-Mg-Zn-Cu series) aluminum alloys can also be applied to body materials. In recent years, 6000 series and 7000 series high-impact aluminum alloys have been used to develop thin plates and hollow profiles, which not only have light weights, high strength, good crack resistance, but also good molding performance. They have been widely used in automobiles.
1.3.2
Other aluminum alloy structural parts
Aluminum alloy is also widely used in other parts of the car, such as manufacturing bumpers' reinforcement brackets of Smure cars by General Motors by using 7021 aluminum plates, producing bumpers' reinforcement brackets for Lincoln Town's car by Ford. Aluminum alloy materials are also applied to automotive suspension parts, which effectively reduce the weight of corresponding parts and improve the smoothness and stability of the driving automobiles, such as disc brake jaws and power transmission frames made from 6061 forgings. Moreover, aluminum alloys are also widely used in automotive air conditioning systems. For example, Japan uses 6595 aluminum alloys to manufacture automotive radiators and refrigerator radiators.